HPC—Hybrid Pulse Control Optismised for all position welding
THE HYBRID PULSE CONTROLS PROCESS
HPC——Hybrid Pulse Control process is synergetic waveform controlled welding process control variants applied in MIG welding. which are Pulse (spray arc) and short-circuit transfer types in one duty cycle. It adopts the smooth switching technology of short-circuit and pulse. By alternately outputting pulse and short-circuit current, the molten pool is heated and cooled periodically, forming fish scale pattern. Thus HPC is particularly suitable for all poisition welding, especially vertical up welding.
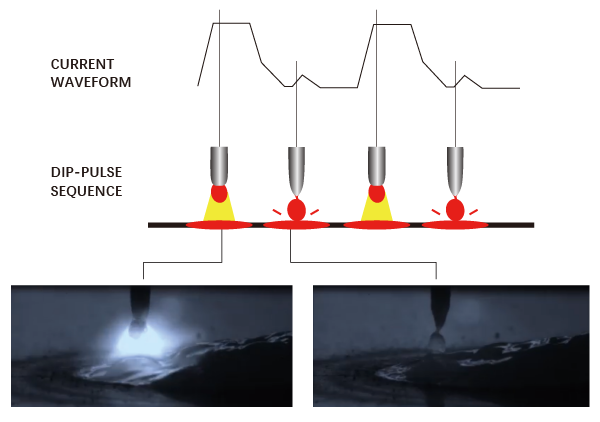
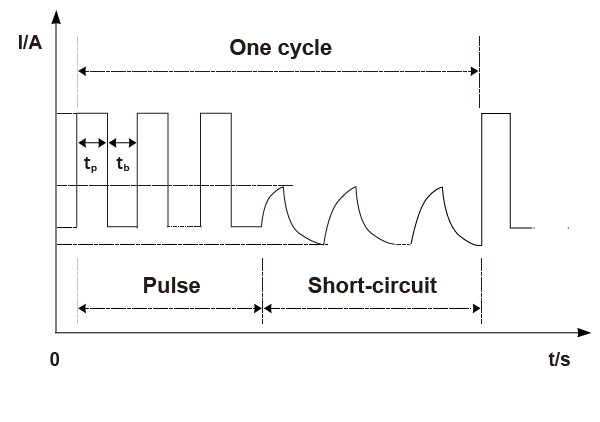
THE ADVANTAGES
Optismised For All Position Welding
Precious heat input and synergetic hybrid waveform controlled process ensured the high productivity during all position welding,especially vertical welding.
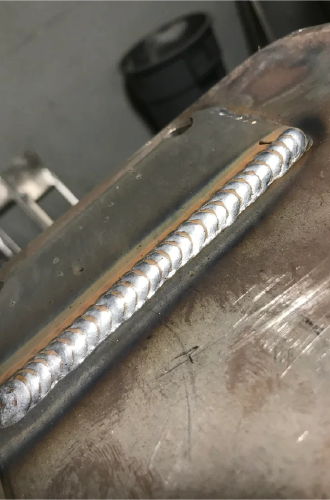
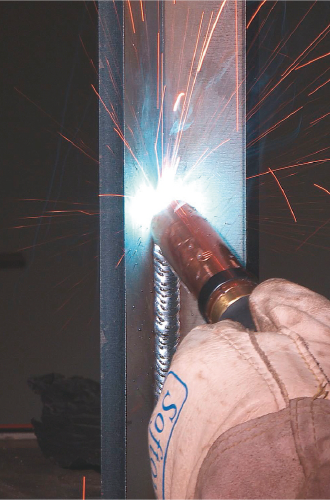
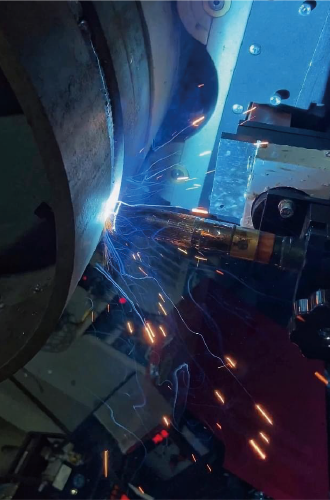
Faster Welding Spped
- Vertical up welding without waving
- simplified user operation
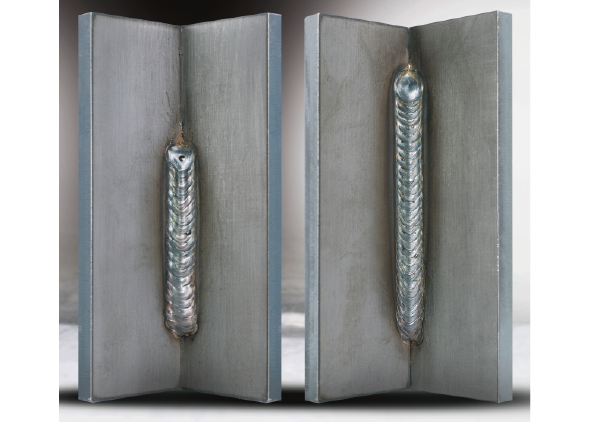
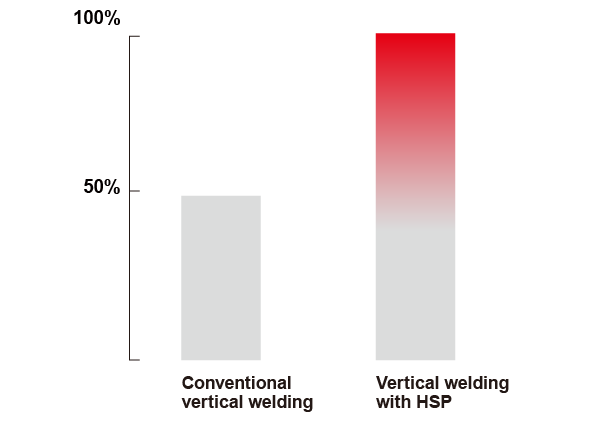
Higher Welding Strength
- Reliable root coverage
- Deep penetration
- Superior throat thickness and edge wetting
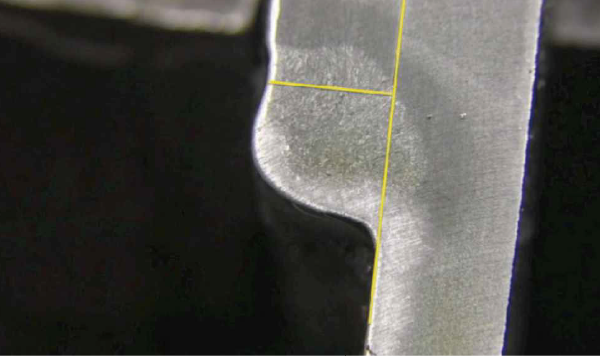
Better Welding Seam
- Fast with minimum spatter
- no undercut defect
- even, slightly rippled weld surface
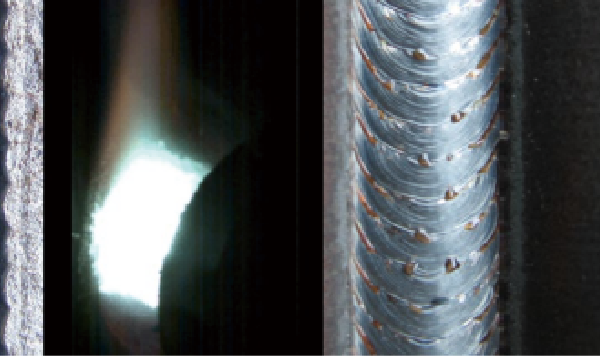
Automation Welding
Continuous movement in the mechanised torch guidance is very good for automation/very simple manual torch guidance.
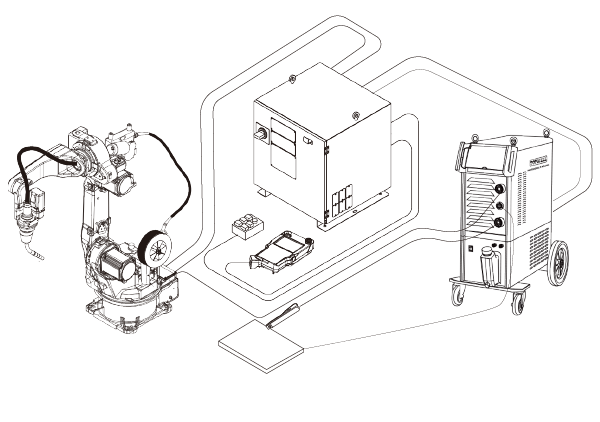
THE APPLICATIONS OF HPC
Designed for welding with robot
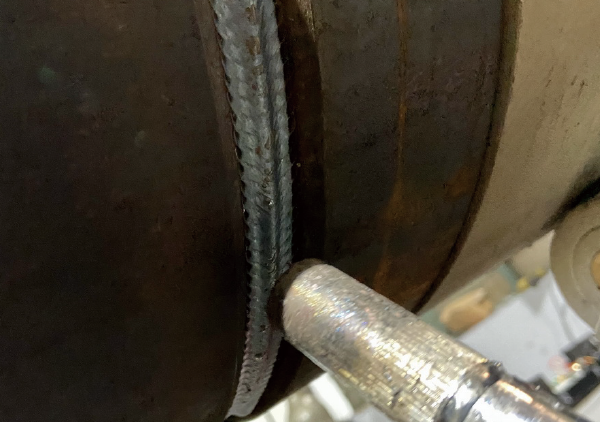
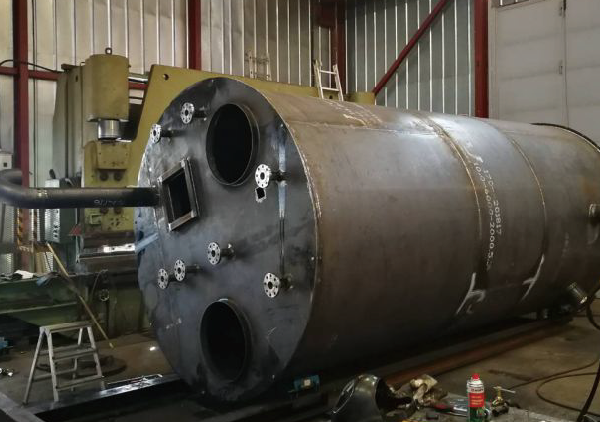