TIPS FOR BETTER GRAM RESULTS
Keep these tips in mind for GTAW applications to help you save time and money in rework and to help ensure a quality finished weld. Taking some extra steps in preparation and setup can help you complete the job on schedule and avoid the cost and hassle of troubleshooting or rework later in the welding process.
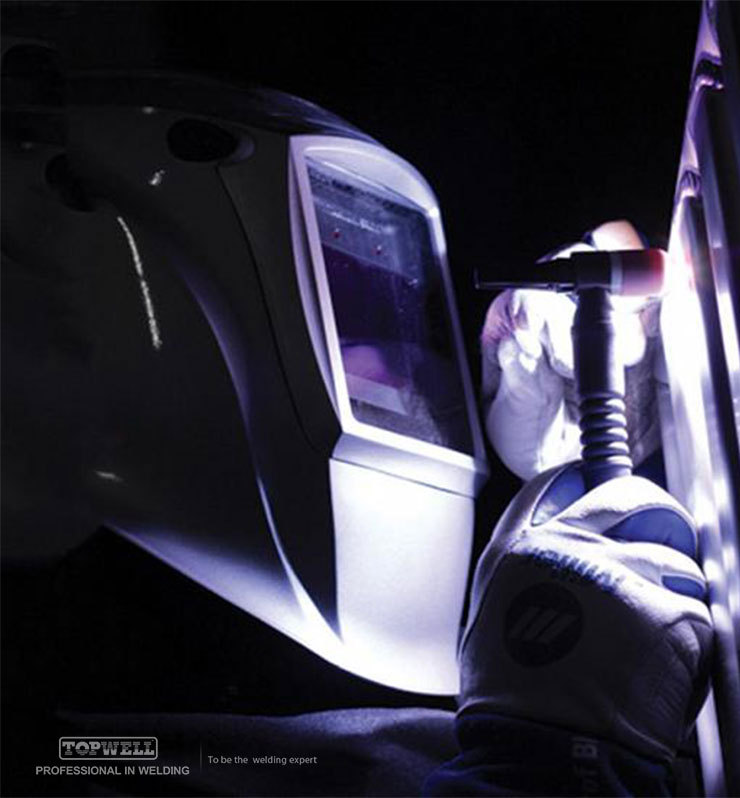
Choosing the right equipment and consumables, and following some key best practices in setup and weld preparation, can help get the job done properly and avoid common problems in GTAW.
Gas tungsten arc welding (GTAW) can present problems that compromise the quality and strength of the finished weld if not corrected. Knowing how to address these issues upfront can reduce the time and costs of troubleshooting, and minimize rework.
Choosing the right equipment and consumables and following some key best practices in setup and weld preparation can also ensure you get the job done properly. Consider these six tips to maximize your success and help you become a better GTAW welder.
1. Know the Material
As with most welding processes, one of the first factors you should consider is the type of material you are welding and its characteristics. It is also critical to know the service conditions the finished weld will encounter.
These factors influence the type of filler metal that is best-suited for the application. For example, if you’ll need to anodize the material after welding it or if the finished product must pass requirements for structural integrity, choose a filler metal capable of providing specific mechanical and chemical properties to support those needs. This factor is even more critical when welding materials like aluminum and stainless steel because of their propensity to distort or crack. Additionally, some materials may require preheat or postweld heat treatment, which can also impact filler metal selection.
When performing GTAW on materials like aluminum, always determine which alloys you are welding in order to choose the right filler metal. Filler metal manufacturers typically offer charts or other tools that provide cross references to most alloys produced today. Such charts also offer suggestions on filler metals based on expected use of the finished product.
2. Select the Right Tungsten
At the center of the GTAW process is the tungsten electrode, a nonconsumable metallic element that carries the welding current to the arc. Knowing your tungsten is key. The thickness of the material being welded and welding amperage are two important factors to consider when making the selection.
Tungsten electrodes come in a variety of diameters, typically from 0.020 to 5⁄32 in., and are available in industry-standard lengths of 7 in. Custom lengths are also available but tend to cost more. The electrodes are composed of either pure tungsten or a hybrid of tungsten and other rare-earth elements and oxides. To eliminate confusion about the various types, each electrode is color-coded at the tip to denote its type.
Depending on the material being welded, you can choose from pure tungsten—typically used for AC welding of aluminum on older transformer-designed machines—or ceriated, lanthanated, rare earth, and thoriated. Each option has characteristics suited for certain applications and materials. Ceriated tungsten is a good general tungsten that can be used with most everything, while thoriated and lanthanated tungsten are good options for welding stainless steel and exotic materials.
Thoriated tungsten provides many benefits because of its high ability to emit electrons, which allows the arc to come off the tip of the tungsten. However, note that thoriated tungsten contains low levels of radioactivity, so be sure to follow the manufacturer’s warnings, instructions, and the Material Safety Data Sheet (MSDS).
3. Keep It Clean
Cleanliness is important in most welding applications, but it is especially critical to GTAW. Contamination can lead to problems such as porosity and cause eventual rework and wasted materials. These factors make cleanliness even more important when working with costly materials such as titanium and aluminum.
Using a gas lens (left), which changes the way gas flows from the nozzle for improved shielding gas coverage and joint accessibility, is one way to ensure you gain the best quality.
You should always clean base materials of oils, grease, and dirt before welding to avoid contaminating the weld. Apply cleaning and degreasing products with a clean, dry, soft cloth. If you are using these products on titanium, make sure the cloth is lint-free. Handle titanium with nitrile gloves, which are resistant to oils and grease. Take caution when choosing a type of cleaner to ensure it does not contain any chlorine, as this can cause severe health problems from fumes created by the welding arc.
Handling filler metals appropriately is important too. Keep cut lengths clean and dry and stored in closed containers. A controlled environment is important to help prevent oxidation of these filler metals. Proper storage of base materials is another key consideration. For example, aluminum base material pieces should always be stored upright and not laid on top of each other to minimize the risk of oxidation.
Avoiding cross-contamination is also important. The grinding dust from a previous piece of material can easily contaminate the weld. Use designated grinding wheels and brushes for each type of material to prevent this problem. In addition, note that grinding dust from titanium and magnesium can be flammable and can contaminate other pieces. Take care to set up grinding for these materials in a separate area and away from open flames.
4. Clamp to Prevent Distortion
Proper clamping of the base material in GTAW applications is a key step to preventing distortion and other issues. The thinner the base material, the more important proper clamping becomes. Clamp the piece in several locations when possible to prevent sections from lifting, and keep the part as square as possible. Some parts may be more difficult to clamp than others.
A third hand can assist in holding the part steady for welding, so consider using one to help with stabilization. A third hand can come in many different shapes and designs, but it is typically a heavier piece that lies or leans on a part and holds it in place for welding. Also, building a support structure can help you keep a steady hand during the welding process. Using a support to lean on or rest your elbows on during welding can help you maintain steadiness for consistent welding.
These preparations may seem time-consuming, and in some cases may take longer than the actual welding, but they are critical to create a steady support that eliminates unintended part and operator movement.
5. Test Weld When Possible
To help ensure that all preparations are correct, you should perform a test weld on similar materials when possible. The more critical the piece, and the more expensive the material, such as titanium, the more important it is to conduct a test weld. Taking the time for this step in the process can minimize problems later, which is especially important on one-of-a-kind pieces or critical welds. Using similar materials for a test weld also helps with accuracy and gives you a feel for how the material will respond to the welding parameters.
Similar to clamping, test welding is an additional step in preparation that pays off in benefits later in the welding process.
The gas coverage on the material has a direct impact on the weld. Using a gas lens, which changes the way gas flows from the nozzle to improve shielding gas coverage and joint accessibility, is one way to ensure you gain the best quality.
4. Clamp to Prevent Distortion
Consumables on the front end of a GTAW torch include the gas cup, the collet, the collet body, and the back cap. A gas lens replaces the collet body that is standard in a GTAW torch. A standard collet body typically has four holes to distribute gas. In contrast, a gas lens has a fine screen that gas flows through to evenly distribute the shielding gas around the tungsten and along the weld puddle and arc, similar to how an aerator on a faucet changes the flow of water.
A gas lens provides much better gas coverage over the weld pool, which is important when welding metals such as stainless steel, titanium, and INCONEL®. Gas lenses provide benefits when welding steel and aluminum too. When you encounter applications that require extra gas coverage or better accessibility to complicated joints, a gas lens also lets you extend the tungsten further to reach the weld. Note: Using a gas lens requires larger-diameter cups to fit over it.