Home / All / Plasma Cutting / All Product /
MAX200 High-Definition Plasma Cutting System with Extra Productivity
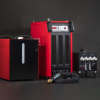
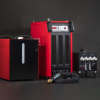
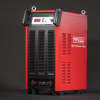

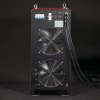

MAX200 High-Definition Plasma Cutting System with Extra Productivity
The HD-MAX plasma systems deliver high performance cut quality with Maximized cutting speed.
Detail Information
DETAILS
MAX200
Extra-Definition, Maximized productivity across a broad range of application needs, from very thin to heavier thicknesses.
Cutting Capacity
Mild Steel Cut Capacity
|
Thickness
|
Dross free*
|
25mm |
Production pierce
|
32mm
|
Maximum cutting capacity | 50mm |
Superior Cutting Performance
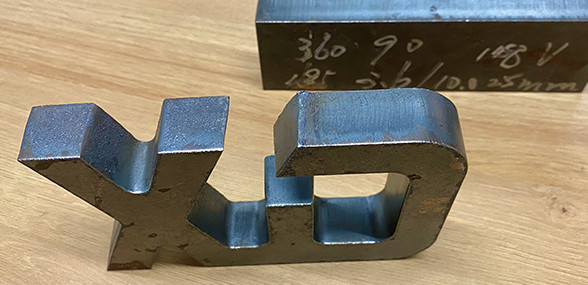
Optimized gas parameters are set and controlled by the software. With Oxygen/Air/N2/H35 plamsa gas, the MAX series plasma cutting system achieves impressive cut speeds, consistent cut quality and exceptional consumable life.
Maximized Productivity
· MAX Series provides faster cutting speed to maximize productivity.
· Engineered with 100% duty cycle for the most demanding production environments.
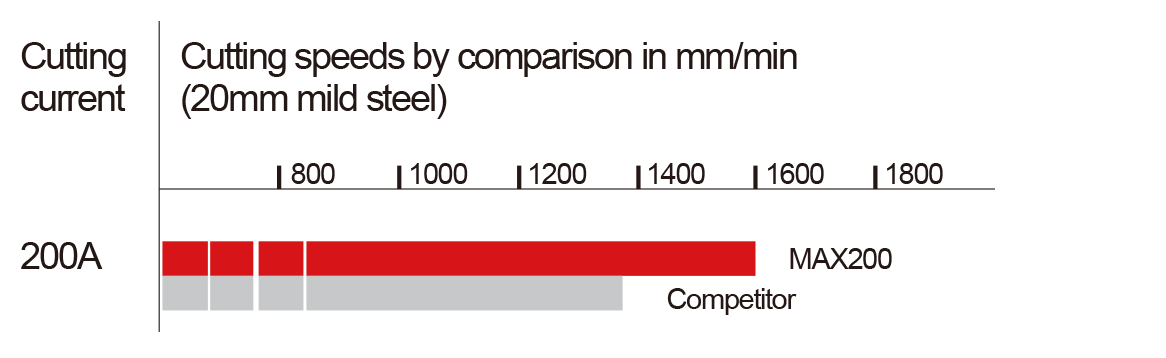
Long-life Consumables
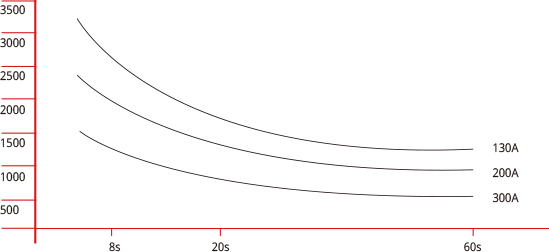
The MAX200 system ramps current and gas flow up and down in a tightly controlled manner to reduce electrode and nozzle erosion.
Reducing electrode and nozzle erosion enables more consistent cut quality over a longer period of time, while providing a significant reduction in operating cost.
· Ignitions per cutting time in seconds
· 20 second duration
· MAX200: 810 times
Efficient Gas Supply
The MAX200 plasma systems significantly increase the efficiency of gas and reduce the gas consumption.
· Cutting Current: 200A
· Gas consumption:
Plasma Gas: 60 l/min
Shielding Gas: 75 l/min
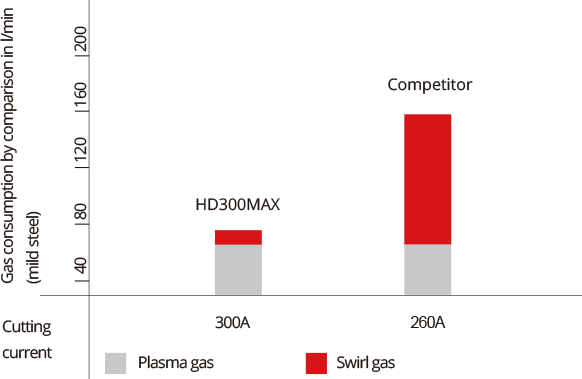
Bevel Cutting Technology
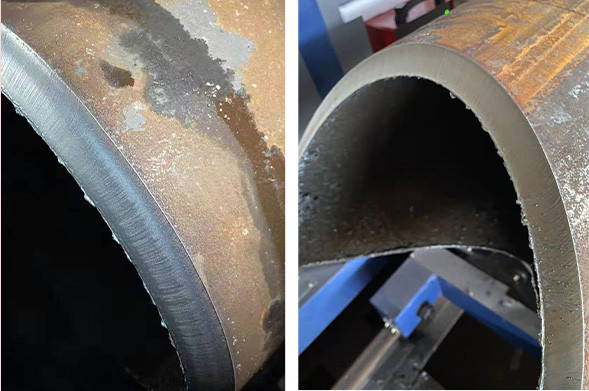
Bevel Cutting Technology is a performance application for mild steel. Factory tested and easily implemented, it takes the guesswork out of the plasma bevel-cutting process. With Bevel Cutting Technology, setups for new jobs are quick and results are accurate and consistent.
· 1 iteration
· Using True Bevel
· Acceptable part and ready to start production
Refined Torch System
· Vented nozzle technology aligns and focuses the plasma arc.
· High Definition Cutting enables powerful precision cutting for superior quality and consistency on mild steel.
· High Definition delivers superior quality to thin stainless steel cutting.
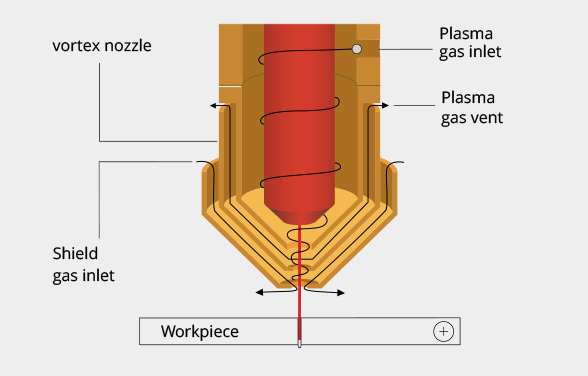
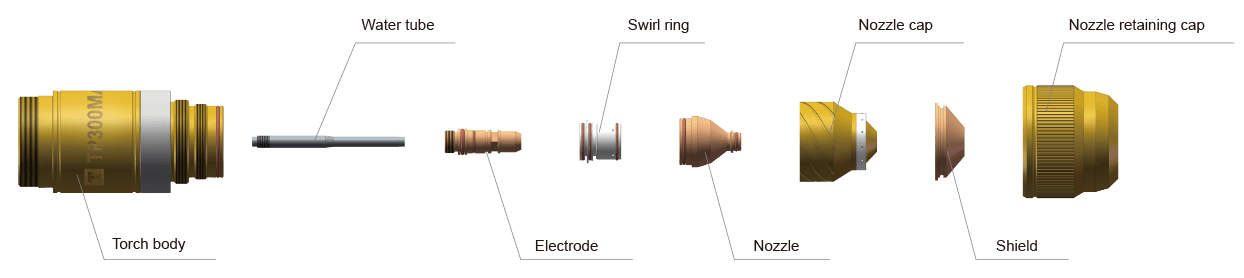
VIDEO
SPECIFICATIONS
Machines
Product Name
|
MAX200
|
Cut angle(ISO 9013 range*)
|
2
|
Weldability
|
Ready to weld
|
Plasma Gas
|
O2; Air; N2; H35
|
Shield Gas | O2; Air; N2; |
Product Weights & Dimensions
Dimensions(L*W*H)
|
960*420*1100mm
|
Net Weight
|
165KG
|
Basic Specification
Input Voltage
|
380V/400V, 3PH, 50/60Hz
|
Input Power
|
50KVA
|
Rated Output Voltage
|
50~200VDC
|
Rated Output(40℃) 100%
|
200A
|
Open Circuit Voltage (OCV) | 430VDC |
* ISO 9013 is a standard that defines cut quality of thermally cut parts. The lower the range (range 1 is the lowest), the smaller the angle on the cut face. Cut angle in range 4 is better than in range 5.
YOU MAY ALSO NEED
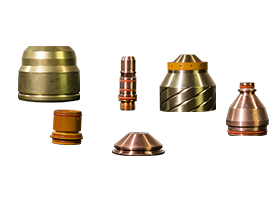
TP300MAX consumable Kit
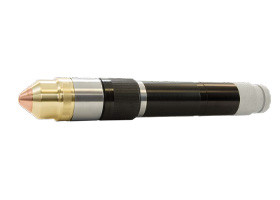
TP260XD
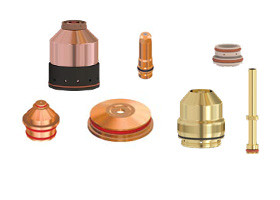
TP260XD Consumable Kit
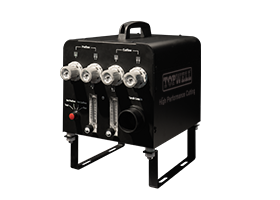
Gas Console (H35/N2)
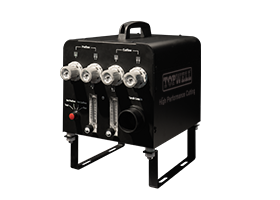
Gas Console (Air/Air)
Related Products
ANY COMMENTS? YOU ARE WELCOME TO LEAVE MESSAGE TO US!
- Tel
- *Title
- *Content
Review
- Loading...